The Pragmatic Manager's Safety Journey
Protect the Team – Safety
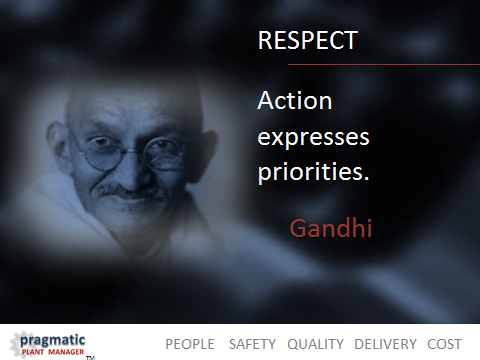
Mahatma Gandhi beautifully articulates why Pragmatic Plant Managers begin their journey pursuing excellence in Safety.
"Action expresses priorities" - Gandhi
Taking immediate action, visible to the associates, establishes respect while reinforcing the importance placed on their safety and well-being.
The safety story will evolve over time. It is not necessary to know precisely where you intend to go before you take the first step of the journey. This may appear to contradict other suggestions for the pragmatic plant manager around the discipline of execution, goal setting and planning. In fact, you are strongly encouraged to act before you develop your Safety Improvement plans – this is aligned with an “act, learn, plan, act-again” approach for continuous improvement.
The first step begins with the Pragmatic Plant Manager. Habits need to change even if current processes are executed well. Our lives change when our habits change. When associates see the Pragmatic Plant Manager’s routine has changed, and is more focused on safety than yesterday, they too begin to change their habits. They see more, they inform more, they take more initiative. The entire organization begins to emulate the newly observed behaviors. Our lives change when our habits change.
Change the daily routine to focus on Safety. Start a daily safety audit today. Plan the overall safety journey tomorrow. Change your habits today – begin (or refresh) walking the floor with the sole purpose of recognizing risks, engaging associates in correction and creating awareness throughout the organization.
The Safety journey consists of:
Leadership Audits
Risk Assessments & Correction
Employee Engagement
Safety Assessment
Annual Safety Business Plan
Leadership Audits:
The first step in the journey is to change the daily routine. Do not be concerned with perfection or accuracy, what is important is a noticeable change in the Pragmatic Plant Manager’s habits. Learn through experimentation. Develop a checklist of safety behaviors expected of managers, supervisors and associates. Describe what’s expected walking through a best-in-class facility that consistently goes injury- free for extended periods of time. Act!
What is done everyday matters more than what is done every once in a while.
The Pragmatic Plant Manager schedules the time each day to assure observations are performed consistently and the ‘urgent’ does not distract from this important task. The impact increases with frequency. Rhythm matters. Remember, our lives change when our habits change. What is done every day matters more than what is done every once In a while.
While on the floor making observations, talk to the associates and describe what’s been seen. Describe the preferred behaviors and why. The ‘why’ should be centered on the health and welfare of the associate. Make a commitment to the associate that unsafe conditions will be corrected. Ask the associate for a commitment that unsafe behaviors will be improved as well. With this simple, but frequent task the first steps of the journey have been taken. A bit of advice – smile. Inquire about their families. You are building relationships. This is your work family.
This is the beginning. You are changing the DNA of your organization.
Disciplinary actions are strongly discouraged.
The audits are performed to generate safety awareness amongst the team and model the expected behaviors. Remember, this is the beginning of changing the organization’s DNA. Care must be taken to assure these first steps of the journey provide a favorable personal experience. Unless a willful, unsafe act is observed that puts the associate or others in jeopardy formal disciplinary action is discouraged. The goal is to create an environment that instinctively surfaces risks so they can be corrected. This is not the time to instill new fears and anxiety amongst the team.
Safety Audit Program:
The Pragmatic Plant Manager prescribes to a philosophy of “act, learn, plan, act-again”. Stay with the audit program for an extended period of time before progressing. This patience will avoid the perception these behaviors are a passing fad. Consistency will send a clear message of the priority placed on a safe workplace. Experimentation and patience affords the opportunity to learn what is most effective for the organization. Learnings provide a platform to work with the leadership team as the program evolves.
After a few months, bring the local leadership team together to discuss the audit approach and its impact on the organization. Document what works well, what does not and what else should be done. Use these learnings to introduce the next logical step in the journey – leadership audits. Formalize a program that requires the leadership team to change habits around safety. Develop a comprehensive audit program aligned with the Safety goals and objectives. Do not stop what’s been started, but enhance the audit program with the involvement of the rest of the leadership team.
Momentum builds. Continue this approach for another few months before introducing additional habits. However, continue to gain knowledge and plan for the third phase – formal risk assessments, while conducting the next iteration of leadership audits and improving working conditions.
Risk Assessments:
Risks reveal themselves through unsafe conditions and unsafe acts. Unsafe conditions are the responsibility of the leadership team and can be corrected with little convincing and are welcomed by the associates. Unsafe acts require a more thoughtful approach and will take more time to impact.
Unsafe conditions generally fall into two areas: facilities & equipment and ergonomics. Facilities and equipment risks are easily identified and ownership for correction resides with the leadership team. Ergonomic risks require additional education for proper identification. Correction requires the leader’s courage to act, redesign of the operator interface to the workstation and the cooperation of associates to change behaviors.
The Pragmatic Plant Manager begins the Risk Assessment phase with facilities and equipment to realize immediate improvements and provide visual, concrete changes on the floor. These physical changes become billboards advertising the value placed on the associate’s well-being - billboards creating hundreds of impressions each day.
How to start?
R3 Risk Assessments
Risk assessments begin with a wall-to-wall assessment of equipment for inherent risks. Corrections here will be immediately visible to the organization further establishing the Pragmatic Plant Manager’s sincerity and focus on the associate’s safety and well-being. These corrections are perceived as an investment for the associate’s benefit, rather than the company’s.
Numerous, free resources exist to assist with this step in the journey.
The process should sound familiar by now. Act. Do not worry about precision. Do some basic research (available here) and begin. Inventory your equipment to assure you eventually touch each piece. The Pragmatic Plant Manager found it best to do a wall-to-wall assessment of each piece of equipment looking for the obvious. This accomplishes two goals; it’s a visible action reinforcing the priority toward the associate’s safety and it enables limited resources applied to the more pressing risks that exist. A more exhaustive ANSI B11 TR3 risk assessment for each piece of equipment will be conducted later. Today (as opposed to the hypothetical tomorrow) demonstrate momentum through immediate actions correcting risks identified.
The Pragmatic Plant Manager has found 3 months to be a time period that establishes the new habit and enables the organization to take on new tasks. This may be too long or not long enough. A large percentage of equipment can be improved over this 3 month period. The R3 approach allows you to establish plant-wide priorities and eliminate the riskiest conditions. Do not be prescriptive. Consider what you are trying to accomplish. An alternate approach is to select the highest risk equipment within each work group, This approach would expose more associates to your improvement efforts. Regardless of which approach you select to prioritize the effort, engage your associates in the risk assessments. They learn from the exercise and you get first-hand information from the users that will prove invaluable understanding the risks that do exist.
After a few months of implementation, you will begin the next phase of risk assessments, focusing on ergonomics. This is a continuous improvement journey. Eventually, in a year-or-two, your risk assessments will be more comprehensive. The risk assessment will consider both the equipment risk and the ergonomic risk. Exercise caution moving too fast. These may be new concepts to your organization. The organization will need time to understand each new concept. Integrating too much at one time may create more learning than the organization can handle. Today, be content with the progress you are making. Recognize your organization is better today than it was yesterday. You will be better tomorrow than today – be patient.
Ergonomic Risk Assessment
The author has been exposed to two different, formal approaches to identify ergonomic risks: The Washington Ergonomics (or WE) Assessment and the Humantech® BRIEF Assessment. Both are effective tools to accomplish your goal of reducing ergonomic risks in your operation. The Pragmatic Plant Manager found the Humantech ® approach easier to grasp and engage associates in the risk assessments and corrective actions. In fact, The Pragmatic Plant Manager selected hourly associates to lead the risk assessment and improvement efforts. This provided credibility with other associates and improved their engagement when asked to change behaviors to reduce or eliminate risks.
Our experience found it best to video each operation, using the video to analyze the work content for risks. The initial assessment was then reviewed with the associates videoed to gain agreement on what was observed. This served two purposes; it validated the assessment and engaged the associate in generating improvement ideas. The associate takes ownership once they understand the risk they are exposed to. Often improvements were immediate, awareness is 50% of a solution.
Employee Engagement:
With these three initiatives – audits, Equipment Risk Assessments and Ergonomic Risk Assessments, your organization should be calibrated on risks. It’s time to engage associates to lead the efforts. A few value-added approaches that would align with your safety goals are listed below.
Let the associates develop (5) Critical Safety Rules
Form a Safety Committee to lead the risk assessments
Appoint subject-matter-experts for both ANSI B11 TR3 assessments and Ergonomic assessments
Develop a Behavior Based Safety program led by associates.
Comprehensive Self-Assessment:
The improvement presented above is very brief. It’s likely obvious to the reader much has been excluded – fall from heights, electrical safety, confined spaces, hot work, pedestrian safety, lock-out, tag-out, powered industrial trucks, crane-hoists, emergency preparedness, personal protective equipment, and industrial hygiene to name a few.
Eventually you are encouraged to define expectations for all variables of a comprehensive safety program. Consider developing a matrix that articulates the minimum requirements for each. Expand this to include best practices and your understanding of world-class behavior. Annually, assess your operation on how it performs in each area.
Annual Safety Business Plan:
The annual self-assessment serves as a tool for your team to align on the next steps of the safety journey. The role as the leader of the Safety effort steps further and further back. Safety becomes self-sustaining as engagement penetrates the organization. Allow the team to develop the Safety Business plan using the self-assessment tool for insight.
The Journey:
This is a journey that does not end. The journey itself is your destination. The journey provides the experiences that create a learning environment. The learnings change the habits of your organization and become its DNA. The habits are observable and give your system credibility as customers visit your facility.
While you are on this journey, you cannot neglect the basics. As you develop the Safety Management System and implement throughout the facility – unsafe conditions and unsafe behaviors must be recognized and corrected. Metrics must be monitored. Problems must be resolved. Associate concerns must be answered.
When you believe new habits are forming and the Safety Management System becomes self-sufficient, begin your education and self-exploration toward Quality.